Experts Share Insights on the Crucial Steps for Evaluating, Qualifying, and Monitoring Suppliers in the Pursuit of True Quality.
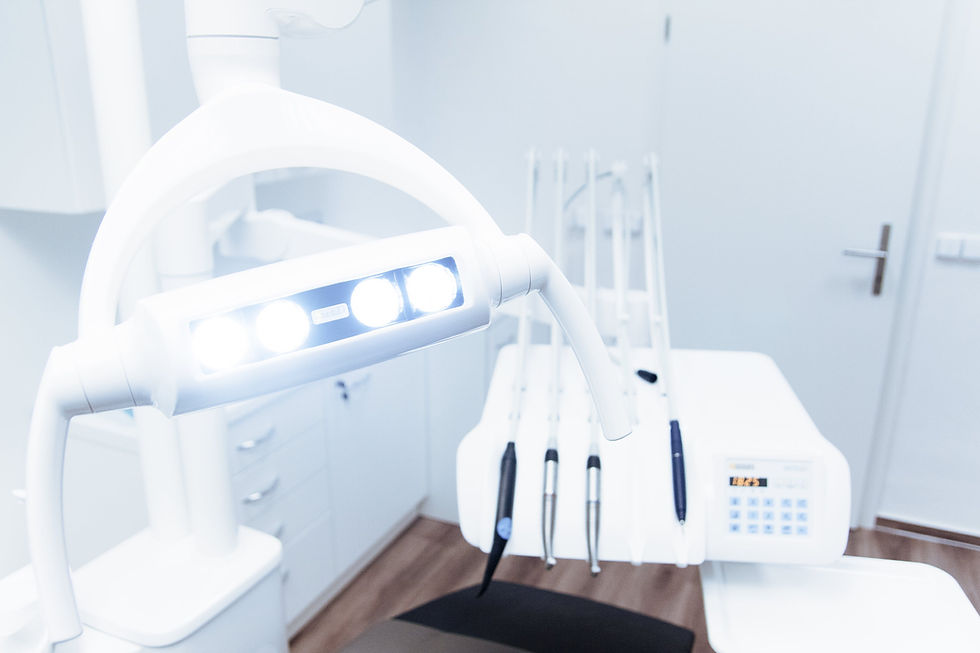
In the intricate world of medical device manufacturing, achieving true quality necessitates a robust foundation in supplier quality management. Three prominent experts in the medical device industry provide valuable insights into the nuances of evaluating, qualifying, and monitoring suppliers, shedding light on the pivotal role this plays in ensuring the highest standards in the sector.
Key Points:
1. Qualifying Suppliers with Care:
Supplier qualification is a meticulous process that begins with the establishment of criteria, evaluation, and implementation of purchasing controls. Rushing through these steps can be tempting, but it's a time-consuming process integral to risk management and ensuring quality in medical devices.
2. Navigating ISO 13485 Compliance:
Jon Speer, founder of Greenlight Guru, emphasises the challenges in building an Approved Supplier List (ASL) in compliance with ISO 13485. The standard requires criteria establishment, objective documentation of supplier performance, consideration of purchased product effects on device quality, and proportionate assessment and monitoring based on device risk.
3. Addressing Scarcity Challenges:
Bassil Akra, CEO of QUNIQUE, highlights the scarcity component in the medical device industry, where unique needs may lead to competition for a limited number of niche service providers. To address this, QUNIQUE introduces the Quality Engine (QE) solution for supplier management, aiding manufacturers in finding compliant solutions for market-ready medical devices.
4. Critical Role of Supplier and Quality Agreements:
Once an ideal supplier is chosen, formal documented quality agreements become essential. Kyle Rose, president of Rook Quality Systems, emphasises the importance of quality agreements that go beyond pricing and sales. These agreements define logistics, business terms, and quality requirements, ensuring clarity in communication, roles, and responsibilities.
5. Ongoing Commitment to Supplier Quality Management:
ISO 13485's risk-based approach requires continual monitoring and validation of suppliers. While the language of the standard may pose challenges, experts like Jon Speer stress the importance of applying a risk-based methodology in supplier qualification. Kyle Rose highlights the need for continuous supplier monitoring to ensure ongoing compliance with quality requirements.
As the medical device industry advances with a focus on achieving true quality, the journey involves a careful orchestration of supplier quality management. From meticulous qualification processes to the establishment of formal agreements and ongoing monitoring, the experts underscore the critical steps that contribute to the sector's commitment to excellence and patient safety.
A message from our sponsors, The Ideas Distillery:
If you would like to look at how to implement an ISO 9001 quality management system, then simply contact us.
Or, if you want to see what's involved in more detail, then get a completely free, no obligation, totally tailored ISO Gap Analysis for your business (only available to UK businesses).
Comments