From Smart Factories to Cloud-Powered Precision: How Data Modernisation Transforms Quality Assurance in Manufacturing.
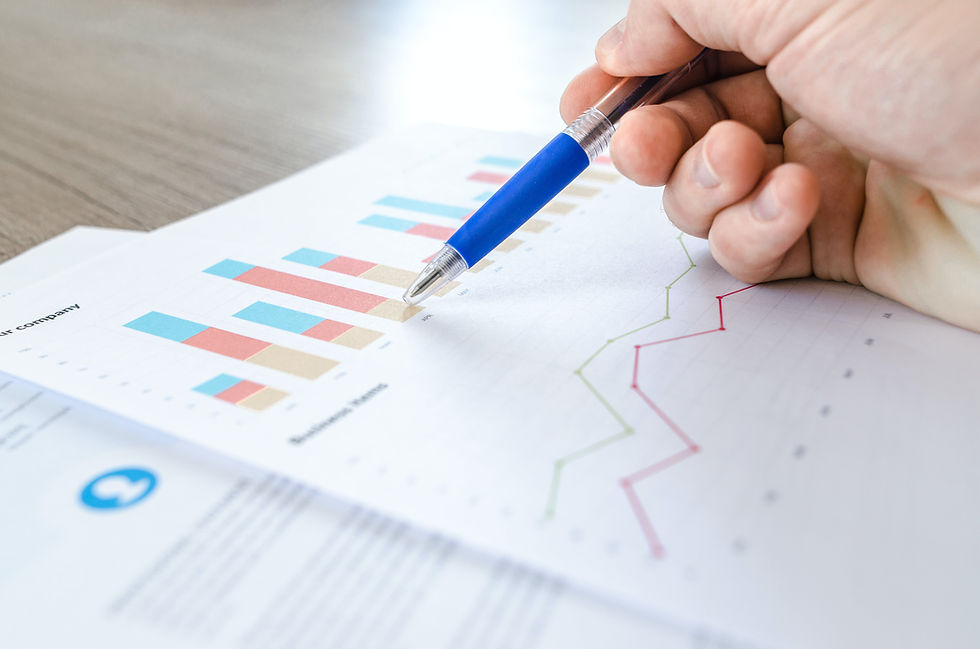
In an era where precision is paramount, the marriage of real-time data and cutting-edge analytics emerges as the linchpin in ensuring impeccable quality across diverse manufacturing landscapes. As products demand infallibility, the journey towards data modernisation becomes imperative, reshaping the very fabric of production processes. One organisation, Greene Tweed, exemplifies this transformative approach, harnessing data to fortify its position in delivering high-performance components for critical applications, including plane braking systems.
Greene Tweed's Leap into Real-Time Precision
Greene Tweed, a pioneer in producing high-performance elastomers and engineered components, has embraced a cloud-based strategy coupled with sophisticated analytics to orchestrate a paradigm shift in its quality assurance framework. By harnessing the power of real-time data, the company achieves a statistical view of its quality system, enabling immediate detection of any deviations from the stringent quality standards. This strategic move aligns with Greene Tweed's ambitious vision of becoming a fully data-driven organisation.
The Foundation: Standardised Data and Cloud Migration
The journey to data modernisation begins with standardising product sets, ensuring consistency in data creation for sales and manufacturing. An instrumental step towards this goal is transitioning to the cloud. By migrating data from system applications and products (SAP) to a cloud environment, companies unlock a responsive system, offering near real-time insights into critical business processes such as work orders, sales orders, and purchase orders.
Consumer Tech Standards Driving Inspiration
Inspired by the immediacy expected in consumer technology, Greene Tweed's cloud environment boasts data that is, on average, two minutes old, with sales data refreshed every 30 minutes—a feat set to further reduce to 20 minutes. This success positions the company halfway towards its objectives, with the impending focus on implementing a comprehensive data governance program across the entire organisation over the next three years.
Smart Factories and Industry 4.0: A Data-Driven Renaissance
Beyond quality assurance, the data-led mindset transforms manufacturing floors into smart factories, a hallmark of Industry 4.0. These connected ecosystems leverage AI, cloud computing, and IoT devices to enhance efficiency, optimise production, streamline operations, and champion sustainable practices. According to Deloitte, the benefits include a 20% improvement in asset efficiency, 30% enhancement in product quality, 30% cost reduction, and a 10% boost in safety and sustainability.
Early Detection, Predictive Maintenance, and Waste Reduction
The influx of data from myriad connected devices not only facilitates early anomaly detection but also enables predictive maintenance. For instance, in Greene Tweed's manufacturing process, any temperature fluctuation in ovens running at 500°F can compromise the final product. Swift identification of potential issues and predictive maintenance ensures product quality and contributes to the elimination of 15-20% of waste materials.
Actionable Intelligence through Analytics Architecture
Building a robust analytics architecture proves pivotal, converging cloud technology and analytics to deliver continuous actionable intelligence from real-time data. This approach empowers organisations to take contextual and timely actions, shaping a future where data becomes the bedrock of ensuring unyielding product quality in an ever-evolving manufacturing landscape.
A message from our sponsors, The Ideas Distillery:
If you would like to look at how to implement an ISO 9001 quality management system, then simply contact us.
Or, if you want to see what's involved in more detail, then get a completely free, no obligation, totally tailored ISO Gap Analysis for your business (only available to UK businesses).
Comentarios